
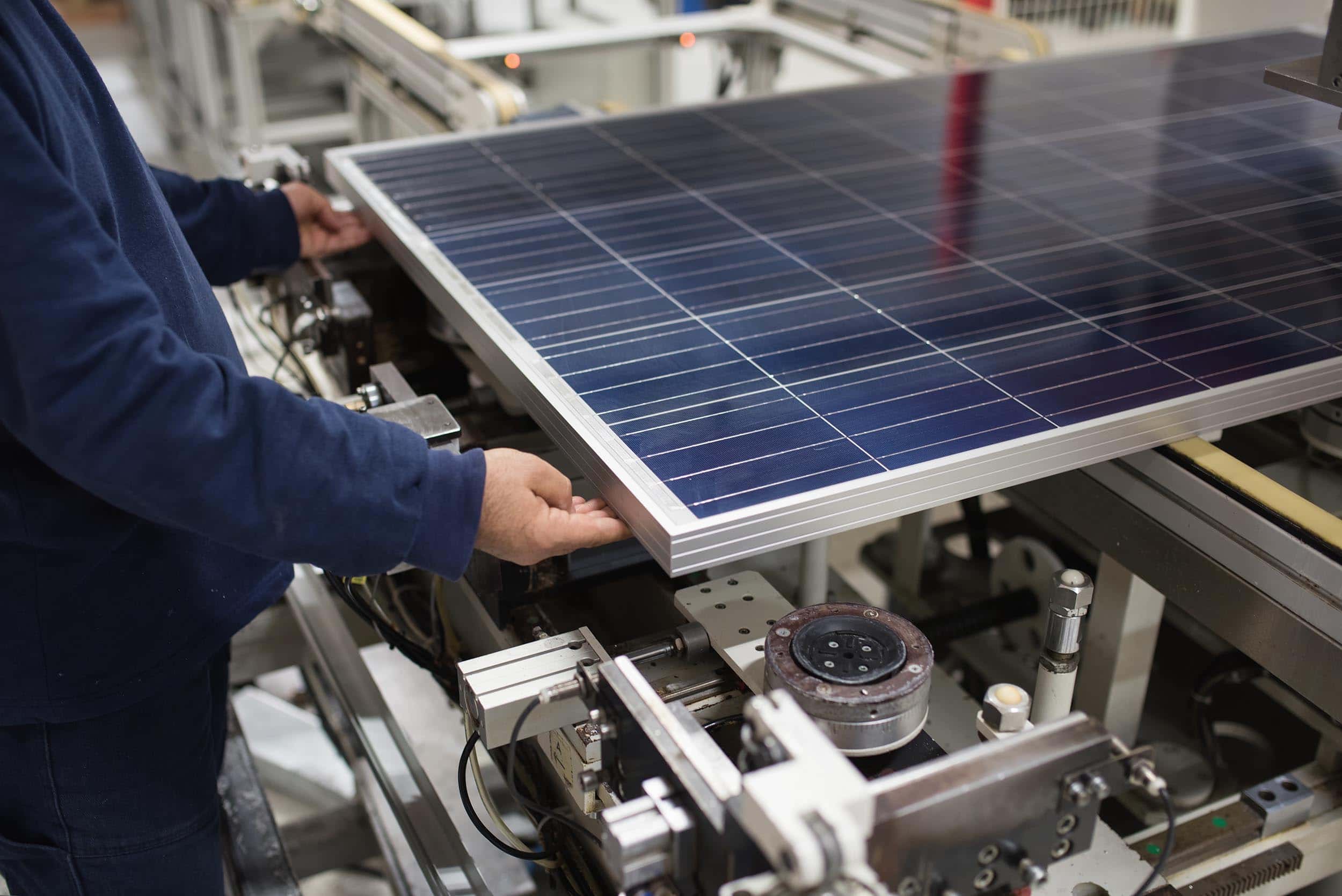

This is due to the size of the material’s band gap which determines how much energy, or amount of photons, is needed in order to produce conductivity and hence electricity. Some cells will have a greater efficiency with longer wavelengths while others prefer smaller wavelengths as shown in Figure 3. In solar cells, depending on the material and technology used, the efficiency when it comes to converting different color bands into electricity is dependent on its spectral sensitivity. Humans can only see the “visible” part, ranging from 400 nm to 800 nm, of the electromagnetic spectrum, where each corresponding color correlates with a specific wavelength. The electromagnetic spectrum consists of the entire range of light with varying wavelengths (λ) and frequencies (v) from radio waves with wavelengths greater than 1 meter to gamma rays less than 0.01 nanometers. The solar panel manufacturing industry is becoming more competitive and is forecasted to become more popular than conventional sources of energy, such as fossil fuels.\] Research and development in the solar energy industry is aiming at reducing the cost of solar panels and increasing efficiency. Again, the ratings of NOCT can be found on the technical specification sheet.Ĭleaning and inspection are the final steps of the production before the module is ready to be shipped to homes or businesses. The parameters used are more close to ‘real life’ scenario: open-circuit module operation temperature at 800W/m2 irradiance, 20☌ ambient temperature, 1m/s wind speed. The ratings will reveal the power output, efficiency, voltage, current, impact and temperature tolerance.Īpart from STC, every manufacturer uses NOCT (nominal operating cell temperature). Electrical parameters are written down and you can find these results on the technical specification sheet of every panel. The tester will deliver the equivalent of 1000W/m2 irradiance, 25☌ cell temperature and an air mass of 1.5g. The panel is put in a flash tester at the manufacturing facility. STC (Standard Test Conditions) are used as a reference point. Once the module is ready, testing is carried out to ensure the cells perform as expected. It is very important that the quality of the encapsulant is high so it doesn’t damage the cells under harsh weather conditions. The use of a frame will also allow the mounting of the panel in a variety of ways, for example with mounting clamps.ĮVA (ethylene vinyl acetate) is the glue that binds everything together. The frame will also provide protection against impact and weather. It all comes together once the frame is assembled. Subsequently, the junction box is added, in order to enable connections inside the module. This will prevent water, soil, and other materials from entering the panel from the back. The backsheet is made from highly durable, polymer-based material. The most common sized system in terms of kWh for UK homes is the 4kWh solar system.Īfter the cells are put together, a thin layer (about 6-7 mm) of glass is added on the front side, facing the sun. The current standard offering in the market are:Ĥ8 cell panels – suitable for small residential roofs.Ħ0-cell panels – this is the standard size.ħ2-cell panels -used for large-scale installations. Solar panels are made of solar cells integrated together in a matrix-like structure. The solar cells are soldered together, using metal connectors to link the cells. The combination of boron and phosphorous will give the positive – negative junction, which is critical for the proper function of the PV cell. This will charge the surface with a negative electrical orientation. In an oven-like chamber, phosphorous is being diffused in a thin layer over the surface of the wafers. The coating will facilitate the absorption of sunlight, rather than reflecting it. This will ensure the conversion of solar energy into electricity. The conductors give the wafer a grid-like matrix on the surface. Each of the wafers is being treated and metal conductors are added on each surface.
